Health and safety
In 2022, the Company updated its key strategic objectives in health and safety for 2023–2025. Efforts in this area are primarily focused on achieving zero fatalities and an industry average injury rate.
Contribution to the UN SDGs
Management system
The Audit Committee deals with industrial safety matters. The Committee reviews management reports on industrial safety performance every quarter, with management participating in the Committee’s meetings, providing detailed account of causes of accidents, measures taken to prevent similar accidents in the future and disciplinary actions taken against the employees at fault.
The Company’s Health, Safety and Environment Committee, led by the Senior Vice President – Operational Director, is focused on improving performance and accountability in health and safety. The Committee meets quarterly at various production sites of the Group.
Remuneration payable to all heads of production units is linked to work-related injury rates. They are personally responsible for the life and health of each of their subordinates. Industrial safety metrics weigh between 12% and 28% in individual KPIs of production site managers. Failure to prevent a fatality blocks performance bonuses. In addition, team KPIs for all employees include injury rate and
Certifications and audits
As at the end of 2022, 47% of the Group companies had health and safety certification.
Certificate
ISO 45001
Certified assets
MMC Norilsk Nickel
Kola MMC
Pechengastroy
Norilsk Nickel Harjavalta
Auditor
Bureau Veritas Certification
In 2022, surveillance audits confirmed compliance of the occupational health and safety management systems of MMC Norilsk Nickel facilities (Head Office, Polar Division, Polar Transport Division, and Murmansk Transport Division) with ISO 45001:2018 international standard. The auditor, Bureau Veritas, noted a high level of maturity and development of the occupational health and safety management system and confirmed the system’s compliance with the standard.
The Group’s production units are also regularly audited for compliance with applicable health and safety requirements. A total of 52 audits took place in 2022 in accordance with the approved schedule, with production site managers and their deputies also involved in the audits.
Work-related injuries
In 2022, the number of fatalities fell to 4 from 11 in 2021, as a result of measures to improve the occupational health management system and the implementation of injury prevention programmes. The decrease was driven mostly by the Norilsk Division, delivering a 4-fold reduction in fatalities, and the Trans-Baikal Division and Energy Division, achieving zero fatalities. Growth in the number of lost-time incidents (66 vs 42 in 2021) was linked to higher transparency in accident reporting.
Two fatalities were caused by rock falls, one in the Kola Division and one in the Norilsk Division. Investigations into these mining accidents resulted in a number of measures: the Company developed and implemented technical measures to support mechanised mining, purchased a face drilling rig and automated temporary supports and conducted a series of audits to monitor the implementation of mine surveyors’ instructions. Another fatality was due to a fall from height when operating a crane. To prevent similar accidents in the future, a multidisciplinary team will regularly inspect bridge cranes, evacuation routes and emergency evacuation equipment. Plans for 2023 include equipping bridge cranes with remote control systems and safe ways to access crane runways. A mine accident that occurred when operating an electric locomotive triggered investigation, resulting in measures to set up transport arrangements for employees to safely access their work area, prevent unauthorised use of electric locomotives and review the mine rail infrastructure repair programme.
All accidents were thoroughly investigated, with the resulting reports submitted to the Board of Directors and action plans developed to eliminate their root causes. Nornickel’s management reinforces the Group’s commitment to achieving zero work-related fatalities and sees fatality-free operations as its strategic priority. The Company continues to implement dedicated programmes to prevent and avoid accidents and work-related injuries. A comprehensive review of industrial safety standards and requirements has been scheduled for 2023 to prioritise focus areas for reducing safety breaches that may result in fatalities or serious injuries.
Contractor risk management
The Company’s industrial safety standards also apply to its contractors.
The increase in work-related injuries among contractors in 2022 was linked to 50% higher staffing levels required to implement major investment projects. In the reporting year, the Company reviewed the general terms and conditions related to occupational health in its contracts with contractors to emphasise the achievement of zero fatalities and the compliance with the golden rules of safety in line with the Company's goals and also to enable contractors to take proactive action on occupational health. In 2022, Nornickel regularly monitored its contractors’ compliance with the H&S requirements, including through joint inspections of compliance with work safety requirements and meetings of health and safety councils (committees) involving contractor representatives.
To improve control and safety of work performed by contractors at its facilities, in 2022, Nornickel updated the standard that sets out relevant requirements for H&S management at all stages. Prior to the commencement of any work, contractor employees are required to receive induction and targeted briefings on occupational health. The standard provides for fines where a contractor’s non-compliance has been identified.
Risk management
The Company has a zero-tolerance approach to unsafe behaviours, as prevention of safety breaches plays a critical role in reducing injuries and accidents.
To keep employees well-informed about safety measures, we regularly develop and update H&S guides, videos, presentations, and other visuals highlighting the most important guidance to protect life and health in various situations or when performing certain types of work.
In 2022, the Company revised its incentives around occupational health performance. Starting from 2023, employees will be rewarded for identifying risks in their workplace.
In 2022, Norilsk Concentrator launched a safety culture transformation project focused on a risk-based approach. The project involved a diagnostic of safety culture and certain processes, a strategy session to identify key systemic measures, training for pilot shops, and a review of the risk identification and assessment system. To date, the project has identified 462 risks, of which 101 have been eliminated and 222 were reported by workers. The project will continue in 2023.
Golden Rules
In 2022, the Company revised and updated its Golden Rules of Safety, using an analysis of fatalities in 2017–2021. Employees who violate these rules are now subject to termination.
Nornickel’s production enterprises have process-, job- and operation-specific regulations and guidelines in place containing dedicated industrial safety sections. For instance, workers with on-site production experience of less than three years wear special red helmets with the word “Caution” on them and protective clothing with “Caution” badges that make them stand out.
Prevention and control measures
Nornickel has developed and put in place an H&S monitoring system featuring multi-tier control with ad hoc, targeted and comprehensive H&S inspections. The first tier control involves the line manager (aided by designated members of the occupational health team) and focuses primarily on workplace set-up. The second and higher control tiers involve special H&S commissions with representatives of management and employees.
In 2022, the incident reporting procedure was changed to accelerate responses, and the incident classification system was improved to enhance further analysis. The investigation and root cause identification process was significantly transformed to further boost accident prevention capabilities.
In addition to the above prevention and control initiatives, the Company has set up and conducts regular behavioural safety audits. The prevention and control team has identified and disciplined over 7 thousand non-compliant employees, including by partially or completely stripping them of their bonuses.
In 2022, Nornickel further improved and integrated the Control, Management, Safety Automated System (CMS AS) into the corporate IT architecture, introducing more than five new algorithms to notify responsible persons via the corporate email, as well as integrating it with related SAP ERP, SAP BW (ACS) and the Nika virtual assistant. In December 2022, the corporate data warehouse was integrated with the Unified System of Corporate Reporting Indicators, enabling rapid generation of annual reports online to deep dive into injury rates across the Group.
Instilling a safety culture among employees
The Company is committed to ensuring its people have all the necessary knowledge, skills and capabilities to perform their duties in a safe and responsible manner.
Training starts immediately after an employee is hired, with a health and safety induction and subsequent on-the-job briefings. Briefings are then repeated regularly in accordance with the existing corporate programmes. There are also interactive training courses for employees in main occupations. In 2022, over 51 thousand Group employees were covered by these trainings and briefings. All Group employees also regularly take online industrial safety trainings and final tests.
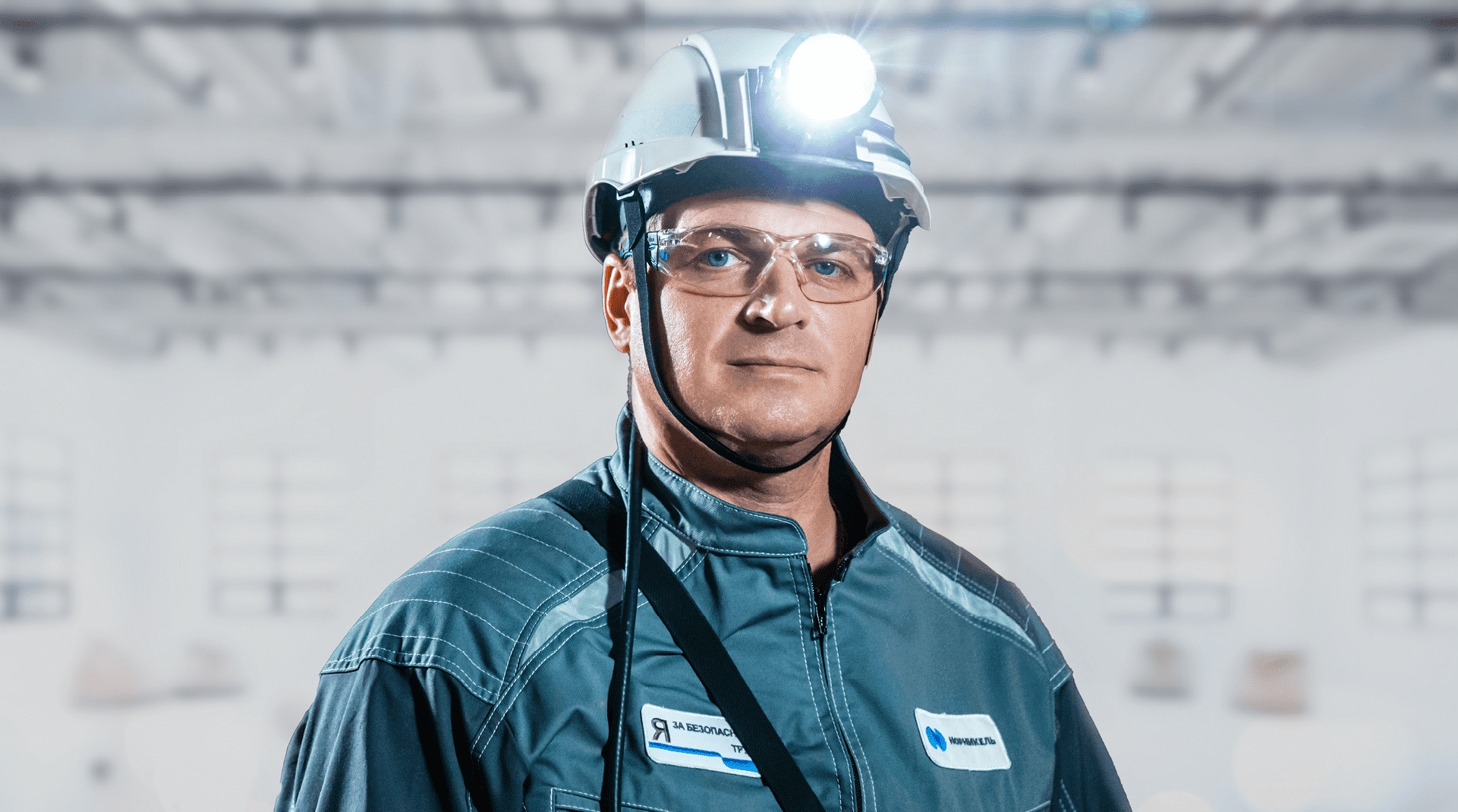
In 2022, the Company launched a project to establish a corporate safety coaching institute. The project covers 18 enterprises with 42 dedicated safety culture coaches among them, currently offering two training courses – Dynamic Risk Assessment for blue-collar employees and Behavioural Safety Audit for line managers. A training course comprises active classroom sessions, engaging all participants, followed by practice sessions in real workplace settings, such as a mine or a production shop. By 2022-end, 750 trainings were delivered to a total 5,268 employees.
Occupational diseases and their prevention
Contribution to the UN SDGs
The Сompany is implementing a large-scale environmental program aimed at reducing harmful emissions into the atmosphere to minimise the risk of occupational diseases. The Company also promotes disease prevention and healthy lifestyle among its workforce, with management focused on communicating to all employees the importance of complying with occupational safety requirements and protecting one’s own health.
Nornickel also seeks to introduce meaningful occupational health initiatives taking into account both workplace and individual risk factors. Production enterprises have dedicated medical aid posts to perform pre-shift health checks and provide medical assistance on request during working hours.
Employees are provided with safety clothing, footwear and other personal protective equipment to mitigate the adverse impact of work-related harm. Employees working in contaminated conditions are provided with free-of-charge wash-off and decontaminating agents.
The Company offers its staff regular disease prevention screening in line with recommendations from the healthcare authorities. All employees regularly undergo mandatory medical examinations paid for by the Company, and special examinations at occupational pathology centres are provided to employees exposed to hazardous substances.
Employees working in harmful and hazardous conditions receive free food, milk and other nutritional products for therapeutic and preventive purposes to promote health and prevent occupational diseases.
The Russian Federal Service for Surveillance on Consumer Rights Protection and Human Wellbeing (Rospotrebnadzor) constantly scrutinises the impact of emissions on the health of the local population in the Company’s operating regions as the healthcare system is almost entirely state-run. Sulphur dioxide emissions in Norilsk have decreased by 30%–35% over the period since Nickel Plant shutdown in 2016. According to Rospotrebnadzor, the total number of newly diagnosed cases in the Norilsk Industrial District decreased by 19% in 2021 (from a 2016 baseline), specifically for disorders of blood and blood-forming organs, as well as other disorders, including the immune system (down 50%), tumours (down 64%) and cardiovascular diseases (down 30%).
Corporate healthcare
The Company has a Corporate Healthcare programme in place to improve the availability of medical care in the regions of its operation for both employees and members of their families. To this end, the Company set up a dedicated subsidiary, Nornickel Corporate Health Centre, and started to roll out its own network of corporate healthcare centres across its footprint, equipped with latest medical equipment and staffed by highly qualified healthcare workers. Under this programme, Company employees enjoy a wide range of quality medical care and timely medical aid services both at its healthcare centres and enterprises.
In December 2021, Nornickel opened its first corporate healthcare centre under the Z-Clinic brand in Norilsk to primarily focus on patients under the VHI programme. The centre currently provides 246 types of medical services across 12 primary care specialties. Over its first year of operation, the centre accommodated about 70 thousand patient visits. The average appointment wait time for many doctors ranges from 7 days to 1 month, which confirms the high local demand for medical care.
In 2022, the Company continued to develop its network and started work of opening two more healthcare centres – in the Talnakh District of Norilsk and in Monchegorsk. Another focus area is a programme to set up smaller healthcare units in remote areas.
The Company is running to establish healthcare centres across its footprint to serve all local residents under the CHI programme. In the reporting year, two new healthcare facilities were repaired and equipped: an MRI centre in Monchegorsk and a healthcare centre in Dudinka. The centres are expected to welcome their first patients in the first half of 2023.
The Workshop Medical Service has started its work, designed to bring quality medical care closer to employees at work and strengthen the prevention of disease detection.
The Company also rolled out its Digital Healthcare programme to implement innovative IT solutions in medical technology. Introduced in 2021 at Zapolyarye Health Resort, the programme was launched in Norilsk in 2022 and is expected to cover healthcare facilities on the Kola Peninsula in 2023. Employees can now use a new mobile app to quickly access their medical records, make an appointment with a doctor and get all the information they need about the clinics’ services. Development plans include fully digitising key medical documents (an electronic health record project), setting up a new automated system for advanced diagnostics and rolling out a disease risk assessment system.
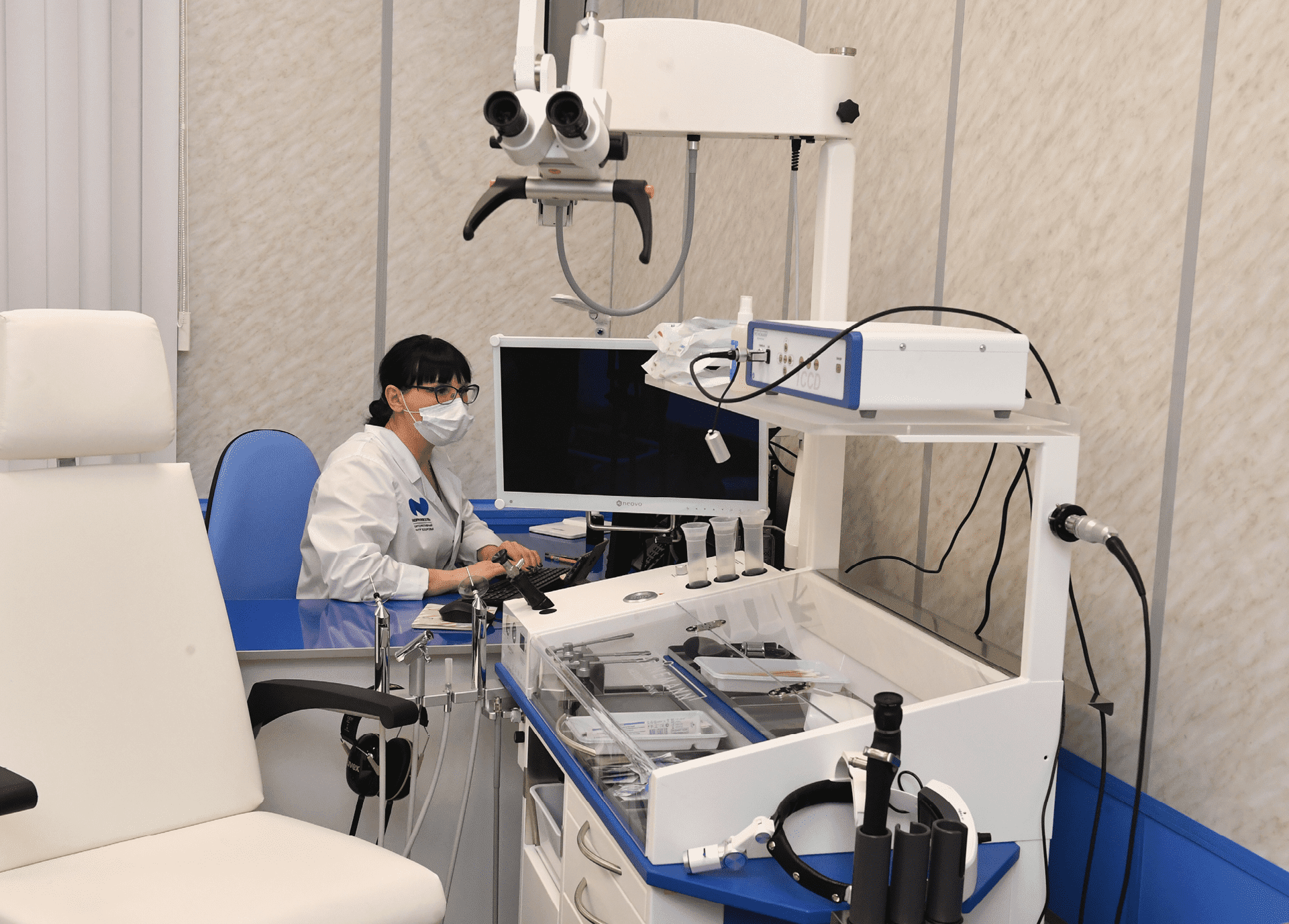