Environmental protection and climate change
Contribution to the UN SDGs
In 2020, Nornickel developed its Holistic Environmental Strategy which sets clear goals across key focus areas: climate change, air, water, soil, waste, and biodiversity. In 2021, the Strategy was further detailed and approved by the Board of Directors, with an update scheduled for the second quarter of 2023.
Nornickel’s Environmental Management System (EMS) is part of the Corporate Integrated Quality and Environmental Management System. This ensures coordination between all environmental matters and other areas, enhancing the Company’s overall performance on environmental safety.
System audit
At the end of 2022, 44% of Group companies (by average headcount) were certified to ISO 14001:2015, an international environmental standard.
The recertification audit conducted in 2021 confirmed the Company’s compliance with ISO 14001:2015, with a certificate of compliance issued for another (sixth) certification period. Following the second surveillance audit of the sixth certification period in November 2022, the auditors concluded that the Company successfully demonstrated that it had deployed and was maintaining and continuously improving its Corporate Integrated Quality and Environmental Management System, as well as confirmed its compliance with ISO 14001:2015.
Our approach
The current approach and further development of the climate risk management system are based on the TCFD (Task Force on Climate-related Financial Disclosures) framework, covering strategy, corporate governance, risk management, metrics, and targets. The Company has in place the Sustainable Development and Climate Change Committee of the Board of Directors, the Board-approved Climate Change Policy and the management-approved TCFD Compliance Roadmap. We aim to be a sustainable and reliable partner. One of our key priorities is to retain a competitive carbon footprint while boosting metals production to enable the global transition to a green economy.
In line with its TCFD Compliance Roadmap, the Company has developed three scenarios of the global economy development and climate change until 2050.
The Company has chosen the Sustainable Palladium as its baseline scenario, according to which traditional industries are expected to continue playing a significant role amid a growing green economy. In particular, internal combustion engine vehicles are expected to retain a large market share, resulting in a steady long-term demand for palladium. The other two scenarios will be used by the Company to stress-test climate-related risks.
Permafrost monitoring
The key risk entailed by global climate change for the Northern climatic zone covering the Norilsk Industrial District includes permafrost thawing, which can significantly reduce permafrost bearing capacity. To minimise such risks, improve the Company’s asset life cycle management and forecast the potential negative impact of higher soil temperatures on buildings and structures, the Company has taken proactive mitigation measures, including:
- measures to identify climate risk factors;
- developing and testing a model to assess the impact of climate change risk factors on the Company’s assets;
- introducing the building and structure monitoring system in the Norilsk Industrial District.
The large-scale automated monitoring programme aims to equip the Company’s buildings and structures with an array of sensors, which will feed real-time data to the main control centre. In total, the programme is planned to install sensors across at least 1,500 facilities in the Norilsk Industrial District.
Key activities implemented in 2021–2022:
- Creating and launching an IT platform to process both automatically and manually collected data from sensors and the Company’s geotechnical monitoring business process;
- Launching systems for automated monitoring of foundation soil temperature, foundation deformations and the temperature and humidity in ventilated crawl spaces across 165 buildings and structures;
- Satellite monitoring of the Company’s assets, which provided a set of data on land surface displacements to bring dedicated management focus to identified issues when conducting field studies of buildings and structures;
- Completing the design of automated monitoring systems for the programme’s Phase 2 buildings and structures (production facilities of NTEC and tailings storage facilities of the Company’s Norilsk Division). Phase 2 deployment of the monitoring system will be completed by 2025.
In 2022, the Company focused on building a research and practice framework for its asset life cycle management strategy. Efforts to this end included drilling deep monitoring wells (200 m) in populated areas of the Norilsk Industrial District to study the permafrost soil temperature range and assess the impact of global climate change on permafrost (including restoring a deep well in the centre of Norilsk, where temperature measurements have been taken since as early as the 1960s). The Company has partnered with leading expert and R&D organisations studying permafrost as well as construction and operation of buildings and structures in northern climates. The Company constantly collects, compiles and analyses data on permafrost soil composition and properties, including historical data from engineering surveys that were carried out in the Norilsk Industrial District throughout its history from the very beginning. Plans include building and implementing predictive models as well as shifting to advanced smart manufacturing technologies, big data processing systems, machine learning, and AI to support decision making around construction and operation of buildings on permafrost.
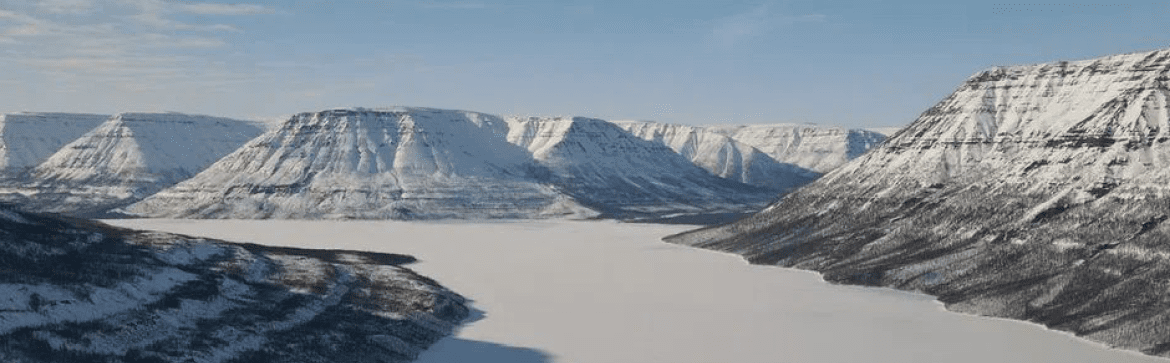
GHG emissions
In 2022, direct and indirect greenhouse gas emissions (Scope 1 + 2) from operations were 8.6 mln tIncluding the emissions allowance for the Sulphur Project and excluding GHG emissions from heat and electricity supplies to household consumers., down 6% y-o-y. The decrease was due to streamlining CHPP operating modes and HPP loads as well as the weather factor – in 2022, the heating period was shorter than in 2021 due to a warmer winter.
Indirect emissions (Scope 2) were calculated using the location-based method, including regional emission factors. Notably, Bystrinsky GOK, the key enterprise of Nornickel’s Trans-Baikal Division, signed an unregulated bilateral agreement to purchase 118.3 mln kWh of electricity to reduce its impact on the climate.
Nornickel’s key production facilities are located in the Norilsk Industrial District, in the Arctic Circle, and operate in sub-zero temperatures for about eight months of the year. Since the Norilsk Industrial District is isolated from the federal energy infrastructure, Nornickel generates electricity and heat locally at its own generating facilities (100% owned by the Group). As a result, the bulk of GHG emissions comes from the Company’s energy assets. At the same time, as Nornickel is the only producer of electricity and heat in the Norilsk Industrial District, the Company also fully meets the demand for energy and heat from social infrastructure facilities and the local population. The share of GHG emissions generated by infrastructure facilities and households in Nornickel’s regions of operation is on average 12% of total Scope 1 and 2 GHG emissions.
Scope 3
In 2022, the Company published its first Scope 3 upstream GHG emissions estimate. Emissions were estimated across all categories of the GHG Protocol. The bulk of the emissions is related to the purchase of goods and equipment from third-party suppliers as well as the consumption of energy and fuel not included in Scope 1 and 2. In 2022, the Company continued to quantify its Scope 3 downstream GHG emissions in line with GHG Protocol. Downstream emissions include those associated with transportation of sold products from the Company to the customer and first use of the product. Iron ore concentrate accounted for the largest share of the total emissions (86%) as its processing is a highly carbon-intensive process. Due to the mix and size of its product portfolio, Nornickel’s Scope 3 downstream emissions are lower than those of its global metals and mining peers.
Renewables and energy efficiency
The Company’s key renewable energy source is hydropower generated by the Group’s Ust-Khantayskaya and Kureyskaya HPPs. In 2022, the share of renewables in total electricity generation stood at 51% for the Group and 56% for the Norilsk Industrial District.
Nornickel has its own energy assets located in the Norilsk Industrial District, in the Arctic Circle, operating in sub-zero temperatures for about eight months of the year. Since the Norilsk Industrial District is a remote area isolated from the federal energy infrastructure, Nornickel has historically been fully self-sufficient in building its operations, including in terms of electricity/energy generation and transmission. As the only producer of electricity and heat in the Norilsk Industrial District, the Company also supplies energy to social infrastructure facilities and the local population.
Natural gas and renewables (hydropower) are the core low-carbon sources for energy generation. Diesel fuel, fuel oil, petrol, and jet fuel are used by Nornickel’s transport assets. Use of coal by energy assets is minimised to only small amounts in certain production processes.
The use of other renewables, such as solar and geothermal energy, is impracticable as Nornickel’s core production assets are located in the Arctic Circle in the Norilsk Industrial District, in harsh climatic conditions. As to wind farms, the Company considered them as part of a feasibility study in 2022. While there are currently no viable options to construct a wind farm in the Norilsk Industrial District, the Company will continue exploring available opportunities.
The Group’s own energy assets produce about 54% of total energy and 83% of electricity consumed by the Group. The Group also supplies electricity and heat to external consumers, primarily local social infrastructure and local communities in the Norilsk Industrial District.
The 7% y-o-y decrease in fuel consumption was primarily driven by reduced gas consumption (down 4%) due to the growing share of renewable electricity and by lower jet fuel consumption (down 92%) due to the sale of NordStar Airlines.
The Group attaches great importance to improving the energy efficiency of its existing and future production sites, focusing on keeping GHG emissions within the declared targets under its comprehensive environmental programme. In 2022, the Company invested more than USD 450 million in upgrading its energy infrastructure. The investments cover a wide range of projects related to equipment replacement at thermal and hydropower plants and upgrades of fuel tank storage facilities, power grids and gas pipelines.
Electricity savings totalled 111,759 thousand kWh in 2022, with 45 energy-saving initiatives implemented.
High sulphur dioxide emissions from the smelting of sulphide concentrates with high sulphur content are a key environmental issue for the Company.
OUR TARGETS
Nornickel’s strategic plan is to transform the Company into an environmentally clean and safe business by implementing Sulphur Project 2.0 across the Norilsk and Kola Divisions and thus cutting its sulphur dioxide emissions.
- Smelting shop Nikel (shut down in December 2020)
- Copper refining line Monchegorsk (shut down in March 2021)
- Nadezhda Metallurgical Plant
- Copper Plant
- Nickel Plant (shut down in 2016)
Optimization of smelting operations to cut SO2 emissions in Russia-Norway border zone
Target: 50%Compare to «base» 2015 year.
reduction in SO2 emissions in Nickel town and city of Zapolyarny
Fact
Outdated smelting shop was shut down in Nickel town in December 2020
SO2 emissions were reduced in Nickel town and city of Zapolyarny in 2020
Complete shut-down of the obsolete Copper refining line and metallurgical shop on the Kola Peninsula
Target: 85%Compare to «base» 2015 year.
reduction in total SO2 emissions at Kola Division
Fact:
Metallurgical shop was shut down in March 2021
SO2 emissions were reduced in 2021 at Kola Division
Programme 2.0 project at Nadezhda smelter to capture furnace gases
Target: 45%Compare to «base» 2015 year.
reduction in SO2 emissions at the Norilsk Division facilities once the design capacity is reached. The design capacity is expected to be achieved in 2024
In progress
Launch of Sulphur Programme 2.0 at Copper Plant to capture furnace and converter gases
Target: up to 90%Compare to «base» 2015 year.
reduction in SO2 emissions at the Norilsk Division facilities after the design capacity is reached
Redesign (2023) and in progress
In 2022, the Group’s pollutant emissions totalled 1.8 mln t, up 10.5% y-o-y. The increase was caused by production recovery in the Norilsk Division after a decline in 2021 that followed suspension of operations at Norilsk Concentrator and the temporary shutdown of two mines due to flooding. The Kola Division continued reducing its emissions with the closure of certain obsolete production facilities: total gross emissions were down 18% from 2021.
The Company’s assets are located in regions with sufficient water resources. In 2022, as in previous years, no shortage of water was reported as enterprises and households were supplied with sufficient amounts of water.
Nornickel is extremely careful about its use of fresh water and strictly complies with restrictions applicable to industrial water withdrawal.
Nornickel’s key production facilities use closed water circuits to keep water withdrawal on a relatively low level. Furthermore, the Company never withdraws water from protected natural areas. The water we used was mostly withdrawn from surface and underground water bodies, in addition to third-party wastewater and natural water inflow. The total water withdrawal remained flat y-o-y in 2022. Natural water inflow and meltwater accounted for 17.6% of the total water withdrawal in 2022. All facilities using water have programmes in place to monitor water bodies and water protection areas.
In 2022, 81.8% of all water used was recycled or reused, in line with the Company’s strategic goals.
Nornickel is committed to responsible and sustainable use of water resources and prevention of water body pollution.
The slight increase in water consumption in 2022 was due to the commissioning of new facilities at the Kola Division, the nickel carbonyl section reaching high capacity and the concentrate shipment unit at the Concentrator ramping up to design capacity.
Wastewater discharge into water bodies also does not exceed the approved limits or have any material impact on biodiversity of water bodies and related habitats. In 2022, the Company decreased its total wastewater discharge by 13.4% y-o-y and also untreated wastewater discharge by 32.5% y-o-y.
In 2022, the mass of pollutant discharges decreased by 12% y-o-y. The decrease in wastewater and pollutant discharges was attributed to a lower volume of water inflow into underground workings due to weather conditions.The Company makes every effort to ensure that substance concentrations in wastewater are kept within regulatory limits, with all division-level programmes at the Company containing measures to this end.
Water risk management
The Company’s ongoing procedures to assess the risks of its impact on water resources include:
- wastewater inventory
- monitoring of wastewater discharge volume and quality at discharge sites
- observation of surface water bodies at control points upstream and downstream of discharge sites
- investments in improving the performance of water treatment systems and building new systems
- monitoring of wastewater treatment processes at treatment facilities and implementation of organisational and technical measures to improve treatment effectiveness. .
The Company reuses most of its industrial waste in its own operations as approximately 99% of the waste generated is non-hazardous (hazard class V). Such waste includes rock and overburden, tailings and metallurgical slags. Ore extraction waste is placed in tailings and used as backfill for underground workings and open pits, road fill or for tailings dam reinforcement.
In 2022, the total weight of waste generated increased due to higher mining and concentration volumes as well as the Company implementing a programme to clean up the sites of unused (dilapidated) facilities and dismantle these facilities, which drove the generation of construction waste.
Tailings
Nornickel currently operates six tailings storage facilities: four in the Norilsk Division, one at Kola MMC and one at Trans-Baikal Division.
While all tailings storage facilities operated by the Company are located at a significant distance from production facilities and local communities, Nornickel recognises these facilities as higher-risk assets with significant potential environmental and social impacts. This is why the Company regularly monitors the condition of hydraulic structures and inspects discharge sites as well as adjacent areas.
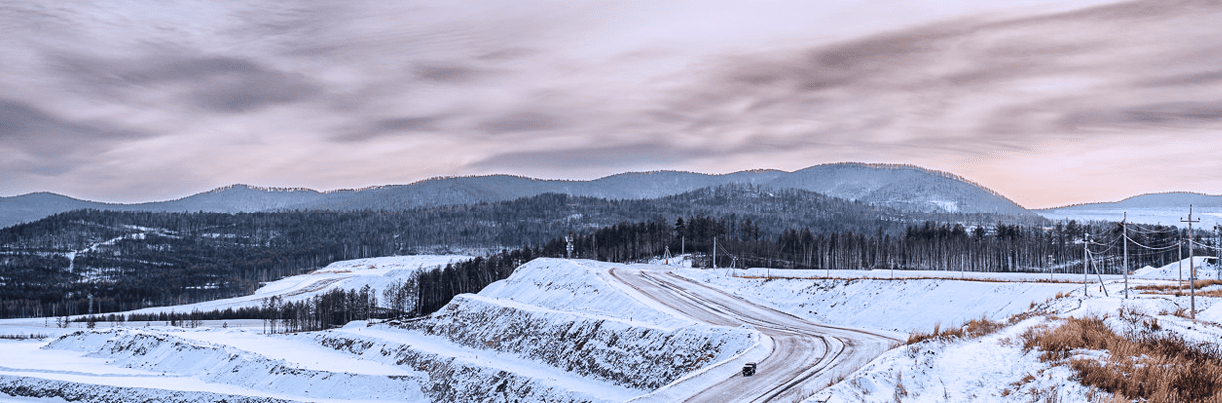
Although Nornickel has for years supported protected areas in its regions of operation, it was not until 2022 that the Company decided to establish a dedicated biodiversity impact management system, also laying the first foundation for it by conducting baseline biodiversity surveys. These studies became another milestone in Nornickel’s history of partnering with scientists for biodiversity conservation.
The baseline survey project, known as the Great Scientific Expedition, was a comprehensive study of the ecosystems near the Company’s operations, including its exploration, mining, concentration, metallurgical, transport, logistics, and energy facilities. Geographically, the surveys covered three regions: the Zabaykalsky Territory, the Murmansk Region and the Taimyr Peninsula, partially including even the Northern Sea Route. This biodiversity survey became the most extensive ecosystem study since the Soviet era. The obtained data were used to establish the key parameters needed to build the system:
- Delineating the areas where ecosystem biodiversity is exposed to negative impacts
- Reference areas, adverse impacts and threats to biodiversity
- Indicator species for local ecosystems
- Biotic and abiotic indicators of ecosystem health
- Key biodiversity values
- The current state of biodiversity within selected affected areas
- Other
For more details on the survey findings, see the Biodiversity section on the Company website.
The expedition will span beyond 2022: it will be continued with in-depth research in 2023, gradually evolving into an ecosystem monitoring programme while also serving as a source of data for assessing biodiversity impacts.
The 2022 survey data were used to establish estimated radii of impact on biodiversity and changes in ecosystem health vs reference areas. This principle was incorporated into the technique developed specifically for Nornickel to check ecosystem health using key biodiversity indicators, with differentiation by impact radius. The technique served as the basis for a methodology to establish the integrated ecosystem indicator (IEI), which will measure the Company’s progress towards its goal of zero net biodiversity losses and zero negative ecosystem changes caused by its production and mining operations. In other words, the IEI will become a tool to track the performance of the biodiversity impact management system.
Starting from 2022, divisions will conduct annual biodiversity monitoring to track changes, and the IEI will also be annually calculated using the methodology and the updated biodiversity monitoring data submitted by each division. The zero net biodiversity losses goal is planned to be achieved through the Prevent – Mitigate – Restore – Offset principle, implementing biodiversity conservation plans.
Such plans will be drawn up to drive the performance of the biodiversity impact management system designed by the Company in parallel with the baseline surveys. To develop this system, a draft corporate Standard for biodiversity conservation was developed in 2022. Next steps for further developing the Company’s biodiversity impact management system include the rollout of the corporate Biodiversity Standard and the development and implementation of division-level long-term biodiversity conservation programmes and annual activity plans based on the standard. The divisions are expected to develop and implement these documents in the 2023 year.
Also in 2022, monitoring was continued for the ecosystems cleaned up after the spill – the efforts known as the “Great Norilsk Expedition”. This was the first large-scale study of biodiversity, which also highlighted the need to study and conserve the ecosystem biodiversity. The data collected by the Great Norilsk Expedition were included in the data analysis of the Great Scientific Expedition.
In a separate programme, the basin of the Pyasina River was studied to explore opportunities for naturally improving the productivity of its water bodies; the results showed a good potential for piloting the latest ecosystem restoration methods.
Another highlight of 2022 was an agreement between Nornickel and the Russian Ministry of Natural Resources and Environment on polar bear conservation, which resulted, inter alia, in two separate operations to rescue polar bears, Dikson and Slastena, with the Company’s management matching any donations to help treat Dikson.
Cooperation with nature reserves
There are no nature reserves in the proximity of Nornickel’s operations. In the Murmansk Region, the Pasvik and the Lapland nature reserves are 10 to 15 km away from the Kola Division production facilities. In the Krasnoyarsk Territory, the boundaries of the Putoransky Nature Reserve buffer zone are at a distance of 80 to 100 km from the Norilsk Division production sites.
The Company regularly organizes volunteer actions, supports nature reserves and finances research of red Book animals, in line with its long-term strategy to maintain biodiversity in its regions of operation and to preserve the unique Arctic nature. In the Zabaykalsky Territory, the Company supports the development of research and technical capabilities of the Uryumkansky Nature Reserve.
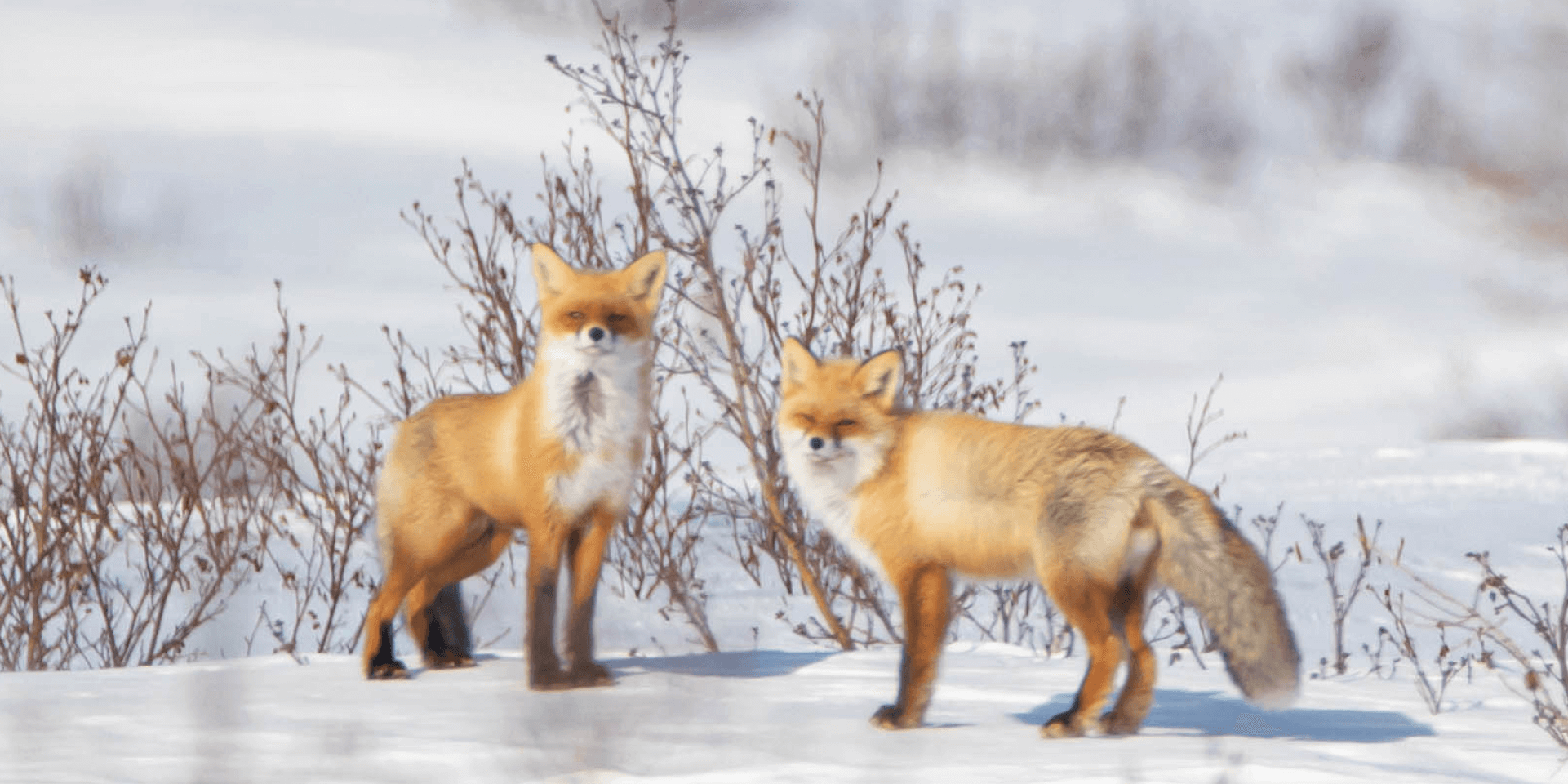